Packaging equipment
Tech & Techniques
The BOTTOM LINE
- Producers seek packaging equipment that can handle format changes
- Automated features appeal in the face of workforce challenges
- Delicate bakery and snack items make robots and cobots popular options
Form and function
When shopping for packaging equipment, snack and bakery producers often pick flexibility, ease of use, and hygienic design.
Neal Lorenzi, Contributing Writer
To improve operations, snack and bakery producers are seeking packaging equipment that offers ease of use, hygienic design, and ergonomics features. They also are looking for adaptable machines capable of handling many product formats and sizes with quick changeover. This need for flexibility is accelerating the adoption of advanced automation, including robotics and fully integrated systems, to reduce downtime and streamline production.
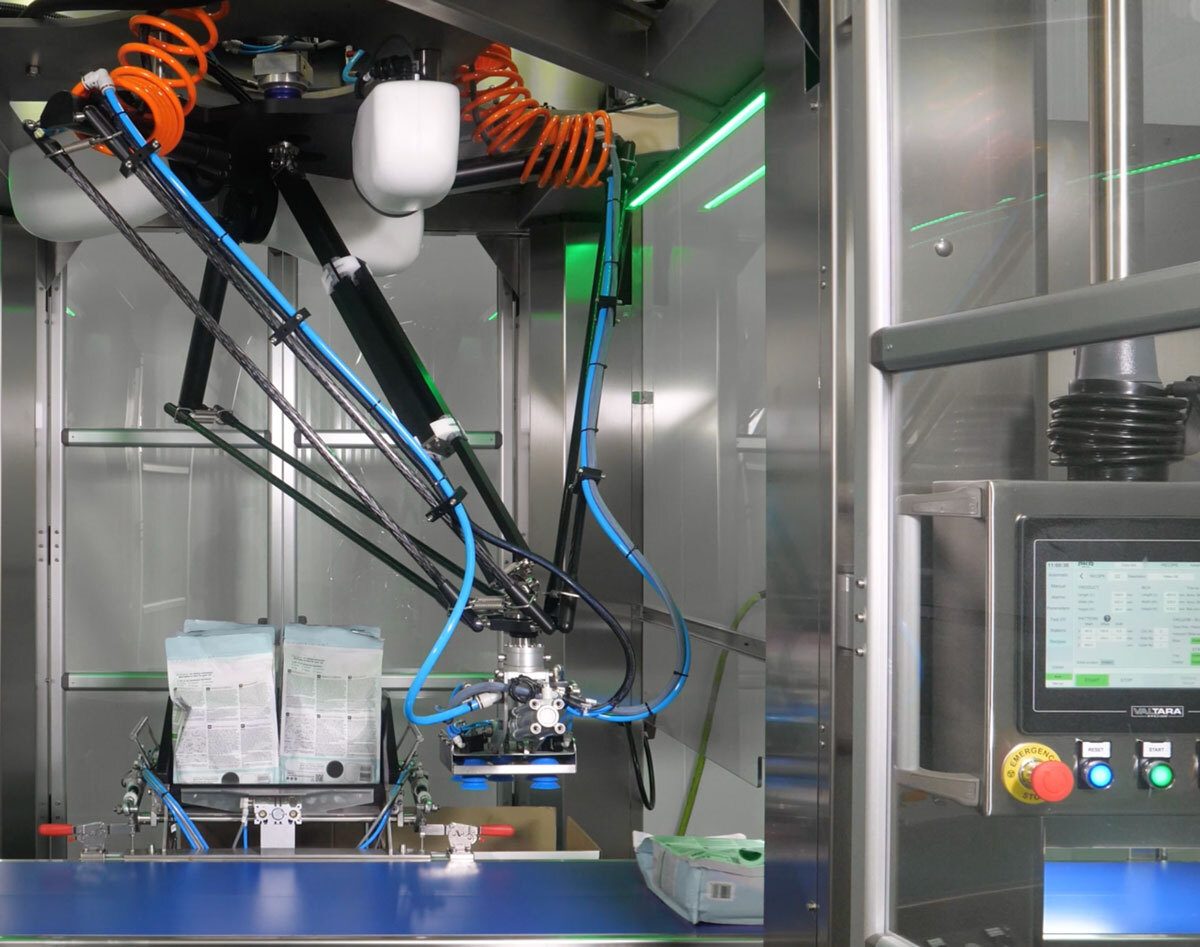
Courtesy of Paxiom
Automatic decisions
Packaging equipment manufacturers are developing integrated systems that improve speed, precision, and efficiency. Innovations such as robotic arms for pick-and-place operations and collaborative robots (cobots) are becoming standard, addressing labor shortages while enhancing safety by minimizing direct human interaction with machinery, experts agree.
Robotics also are being deployed for secondary packaging and end-of-line solutions, where the use of delta robots and cobots allows manufacturers to handle baked goods with precision and care. “This approach ensures delicate items are not damaged while boosting efficiency. The systems significantly reduce labor and space required, streamlining the packaging process and optimizing facility layouts,” says Luis Pilonieta, director of sales at Paxiom Automation Inc.
Packaging equipment manufacturers also are developing machines with advanced human-machine interface (HMI) that provide step-by-step guidance for changeovers, thus reducing errors and saving time. Other innovations include ultra-low roll heights for easier film loading, automated jam recovery systems, and integrated blowers for chain cleaning. “These features not only improve worker safety but also enhance productivity,” says Brantley Turner, global product line leader for VFFS and flow wrapping, BW Flexible Systems.
HMIs also are becoming more user friendly with access to machine features and diagnostics, according to Josh Becker, bakery and confection segment manager at Harpak-ULMA Packaging. “Machine efficiencies are being calculated at real time intervals to show performance while listing areas of the machine where inefficiencies are occurring.”
Worker safety is being prioritized through intuitive HMIs and enhanced guarding systems that comply with safety standards. Many packaging systems now offer remote monitoring capabilities, which allow operators to troubleshoot and adjust settings remotely. In addition, more bakery and snack producers are partnering with complete solutions providers in order to optimize integration across all stages of production.
New approaches
The latest packaging equipment incorporates many of these features. For example, TNA Solutions has introduced the tna ropac 5—a case packing system that is capable of handling up to 200 flexible bags per minute, according to Ian Richards, group solution specialist manager–Packaging. The system features TNA’s semi-rotary bag stacking technology, designed for small-to-medium, pillow-style bags for snacks and bakery items. Also, its tool-less changeover and compact design enable seamless integration into production lines.
“Case packing often represents a bottleneck in production, which impacts the entire packaging line,” Richards says. “Recognizing this, TNA engineered the tna ropac 5 to operate at up to 95% efficiency, even at elevated speeds. This is achieved via its rotary shelves, which gently catch bags in rows before collectively loading them into cases, thus avoiding high accelerations—a critical factor in reducing product damage and maintaining throughput.”
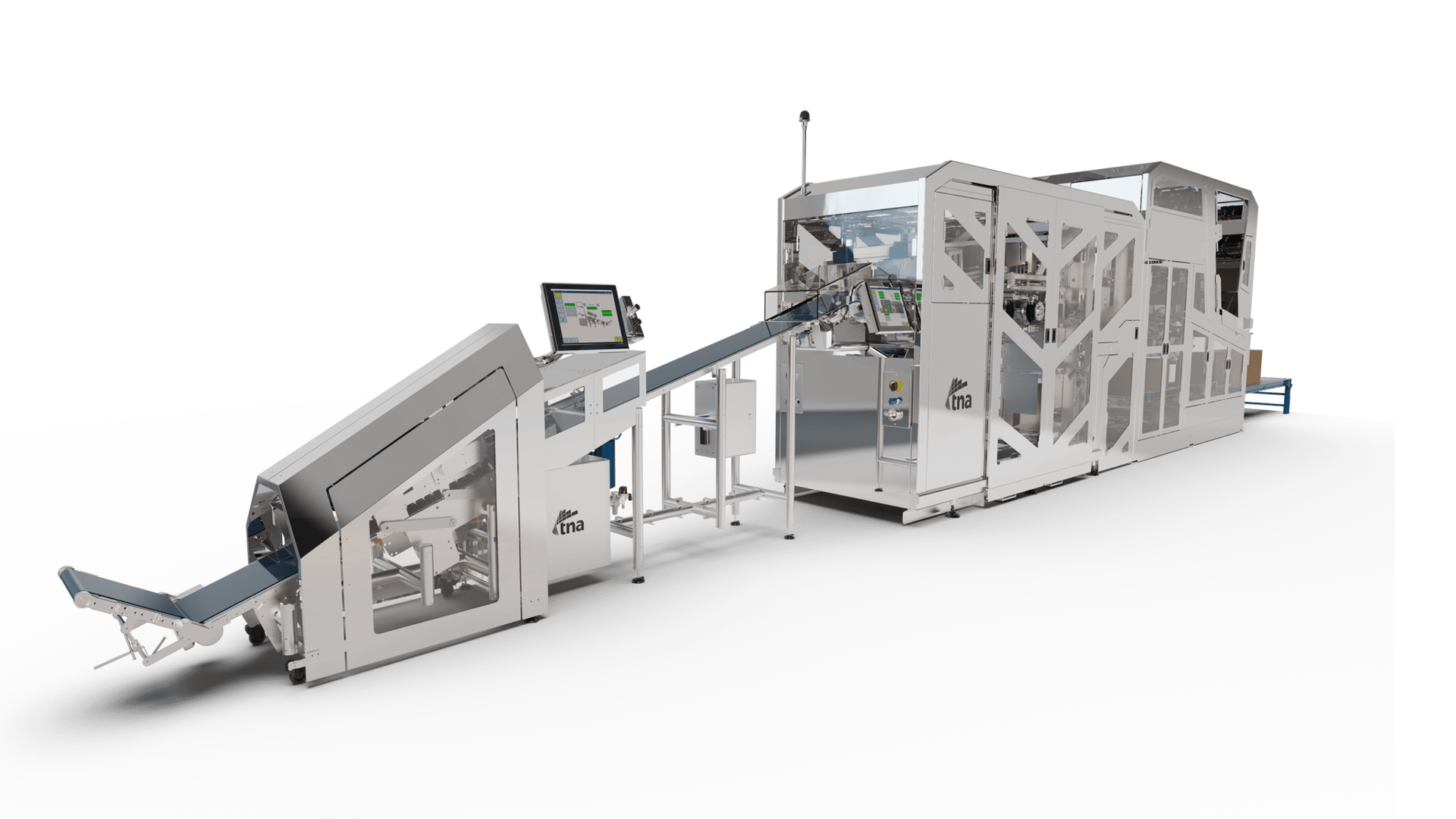
Courtesy of TNA Solutions
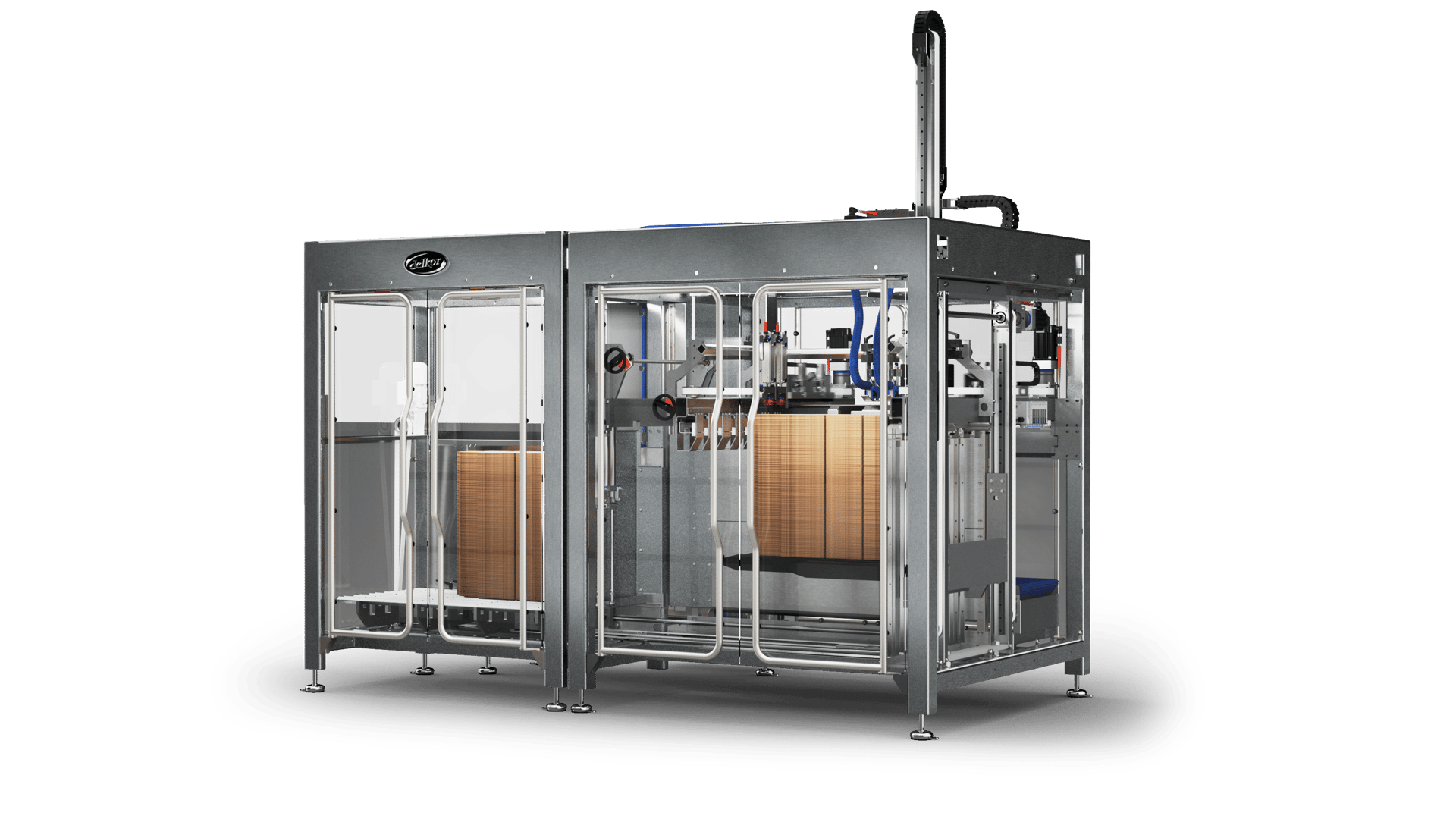
Courtesy of Delkor Systems
Delkor Systems plans to introduce a new generation of Combo-line Bread Case Packers designed as an all-in-one solution for single-use shippers and reusable trays in 2025. “Producers can switch between corrugated (one way) shippers and bread tray formats in the same machine,” says Dale Andersen, president and CEO. “Retailers are moving away from direct store distribution (DSD) trays and into corrugated cases due to the challenges and costs involved.”
Delkor Systems recently introduced Smart-Lock, which streamlines packaging size adjustments using a linear bearing slide, LED-based feedback and an automatic locking system. It reportedly eliminates the need for rotary counters, allowing precise, manual adjustments with minimal effort. “It is three times faster, more accurate and designed to virtually eliminate operator errors,” Andersen notes.
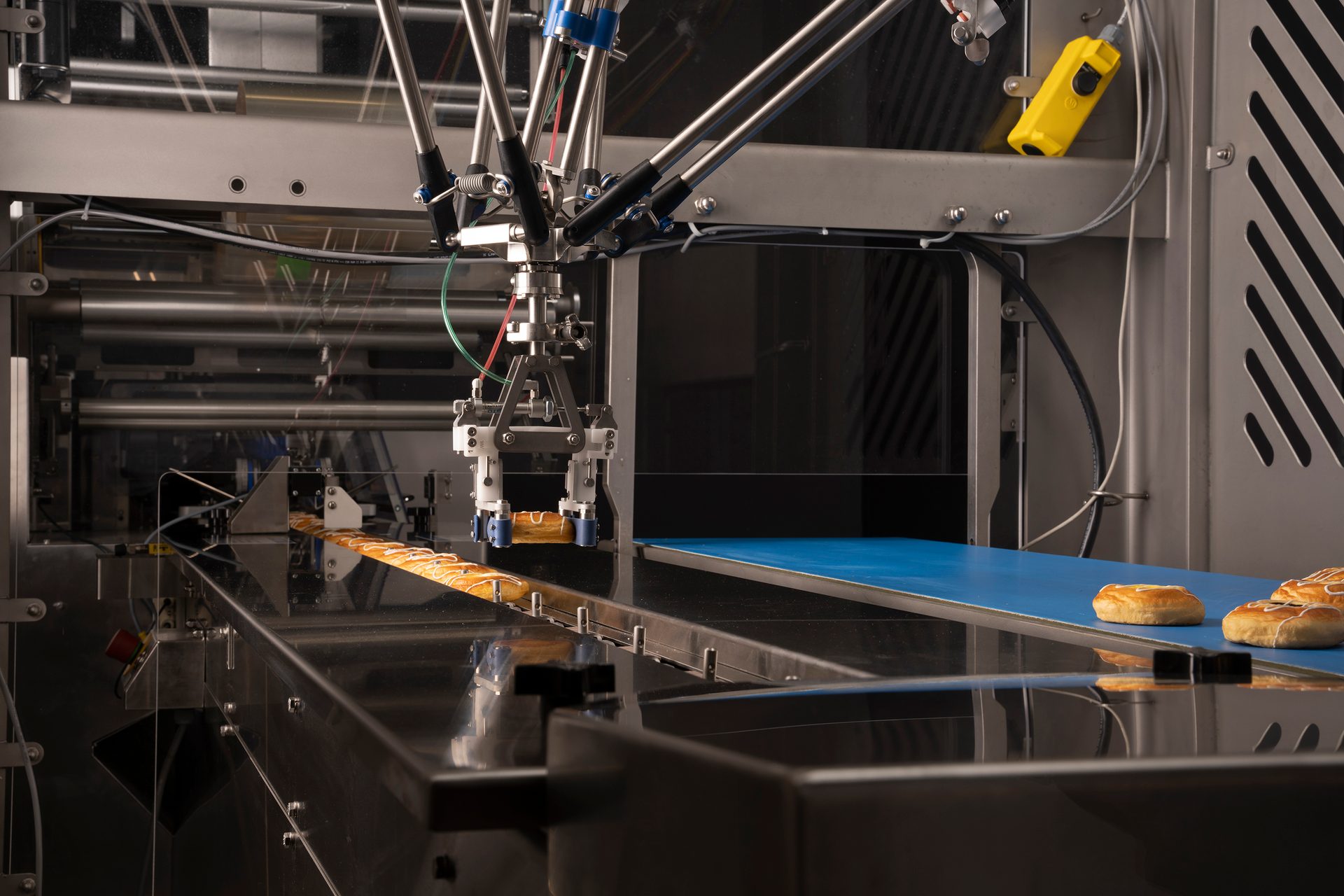
Courtesy of Formost Fuji
“Customers want conveyor belts that can be cleaned more easily.”
— Rudy Sanchez, food handling product manager, Key Technology
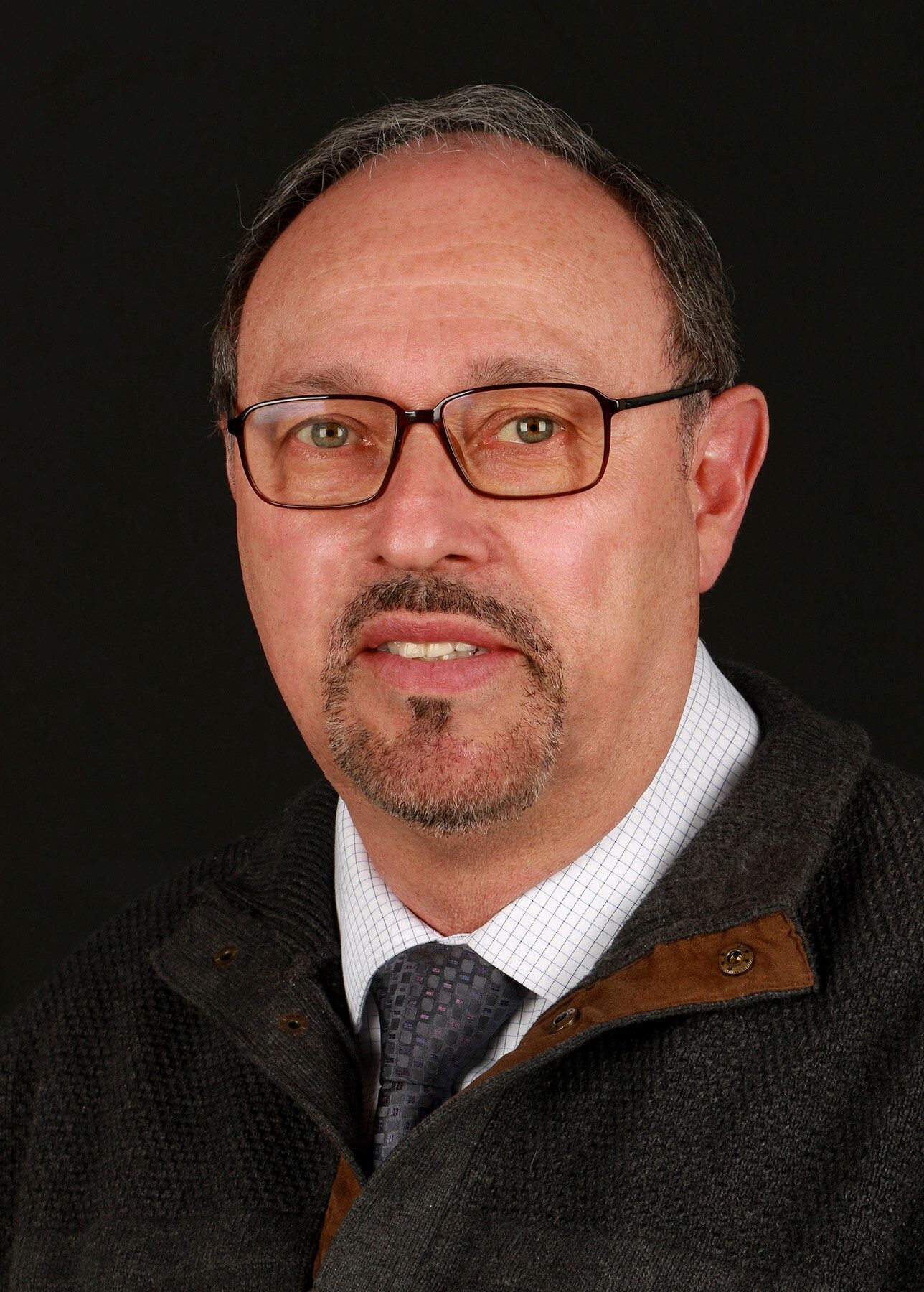
BW Flexible Systems offers the Hayssen R300 flow wrapper, which is designed to boost uptime and simplify operations. “Key features include: intuitive HMI, which provides step-by-step guidance for changeovers; ultra-low film spindle, which enhances operator safety and accessibility; automated jam recovery; and easy cleaning design,” Turner notes. Also, an integrated blower keeps the chain clean during operation.
Formost Fuji offers horizontal flow wrappers (Alpha 8 series), bagging machines (several models, including BDS, GTS and FFB), and automated packaging lines that are built to meet customer requirements. “This means that bakery and snack producers can work with us to build systems that are friendly to their operators and operating budget,” says Angela McDaniel, marketing coordinator.
Paxiom Automation Inc. offer a range of packaging equipment designed to enhance productivity for bakery and snack producers, according to Pilonieta. One is the PKR Delta Robotic System, a versatile solution for pick-and-place operations. The system uses robotics to handle products delicately while optimizing speed and accuracy in secondary packaging processes. Another is the Bag Inserter (Model BI), Case Filler (PrimoLinear V25), and Bag Uncuffer (Model BU). “These systems streamline processes such as bag insertion, filling and un-cuffing.”
Quick changes
Triangle Package Machinery Co. offers the Flex 1 bag-in-box cartoner, which reportedly offers 40% greater efficiency than traditional bag-in-box lines due to its ability to adjust speed on the fly and match the speed of the vertical bagger that feeds it, according to Paul Muskat, VP of business development. “The Flex 1 now features auto-changeover that starts with the push of a button. The machine then automatically adjusts to accommodate different sized cartons.”
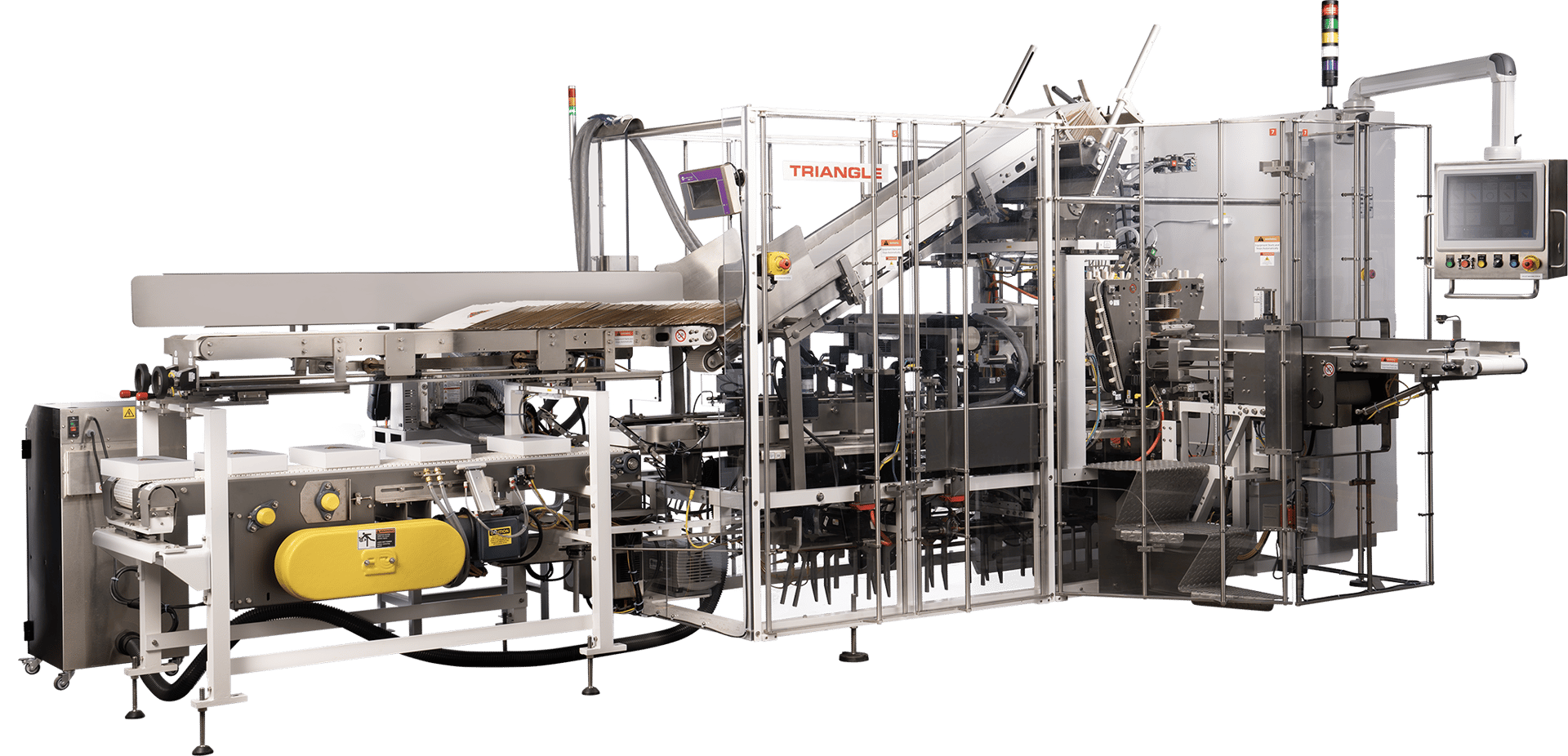
Courtesy of Triangle
Cama North America supplies top-load and end-load cartoning, case packing, sleeving, and robotic integration, utilizing its robots designed for the food industry. The company’s IF299 Monoblock Top Load Cartoning System and Wraparound Case Packer features sanitary design. “The system can pick and place bagged tins with a vision-guided robot, then form, load, and close top-load paperboard cartons and case packing cartons or bagged tins,” says Billy Goodman, managing director.
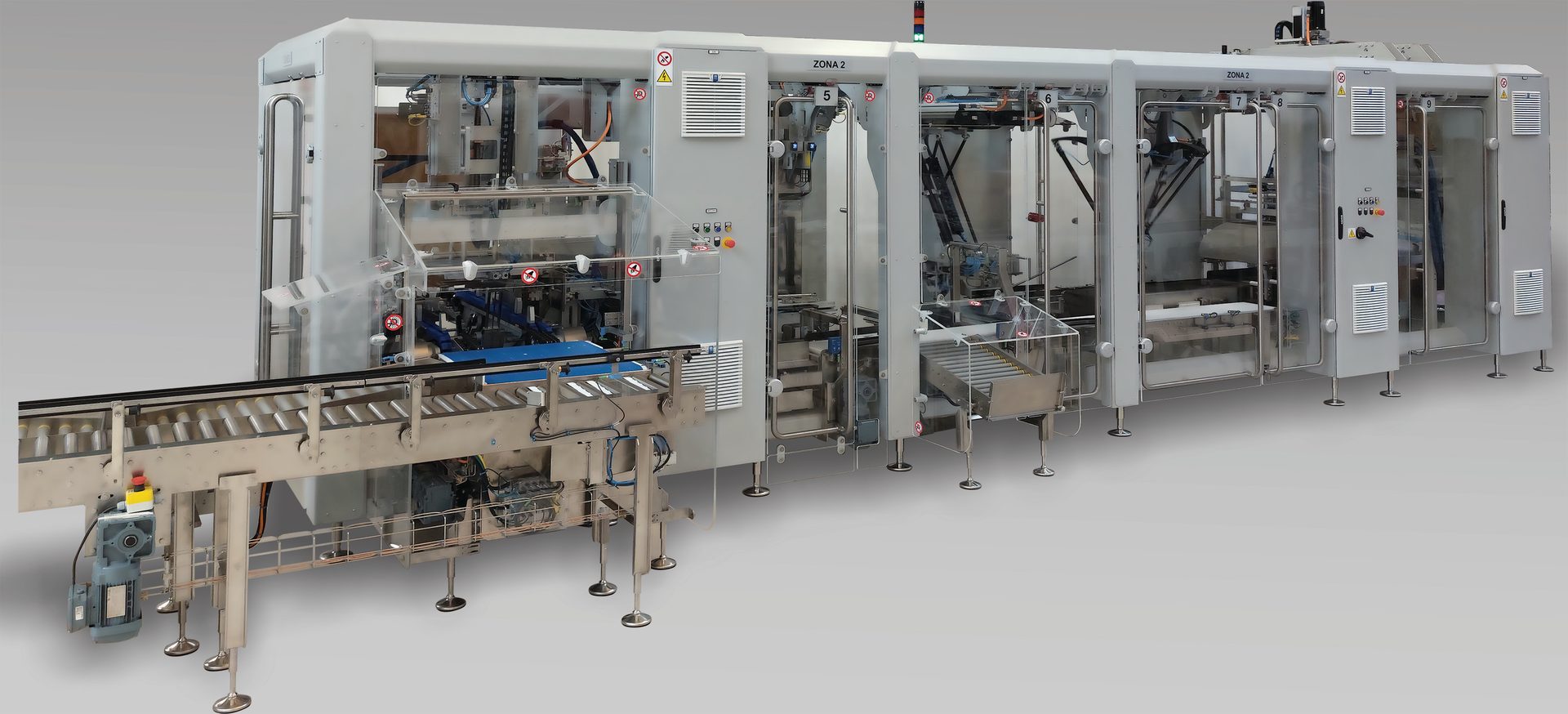
Courtesy of Cama
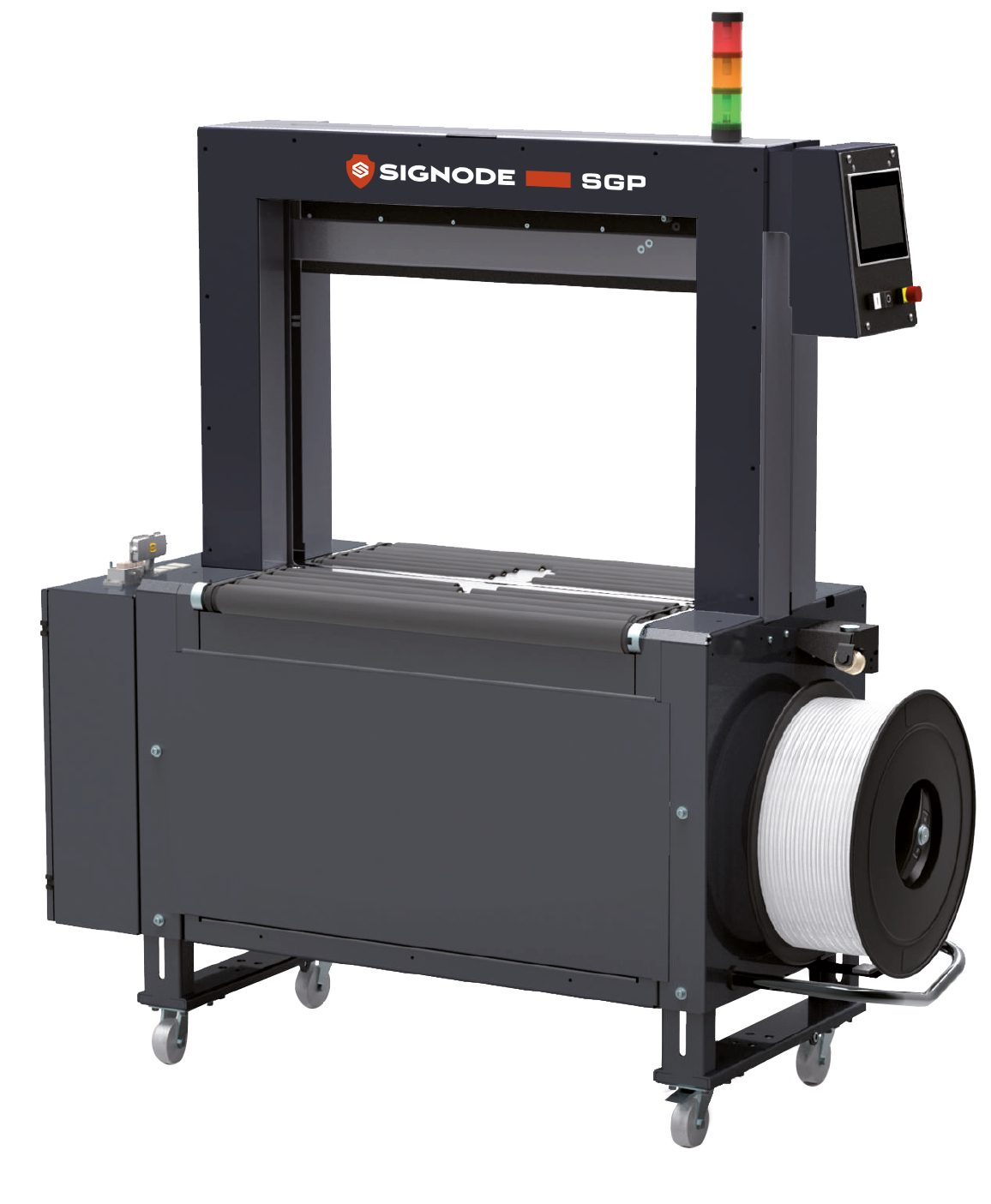
Courtesy of Signode Industrial Group LLC
In the area of strapping, Signode Industrial Group LLC has introduced the BXT4 Battery Hand Tool for Plastic Strapping with EasyTrigger Technology, which enhances ergonomics.
“EasyTrigger facilitates a smoother strapping process by allowing for a quick, motor-supported opening of the tensioning unit,” says Rick Hantke, director of marketing. “The ability to control strap tension at any stage before welding increases flexibility and efficiency, which is crucial for handling the unique packaging needs of the snack and bakery industry.”
Signode also offers the Octopus S Series stretch wrapping machine, which reportedly streamlines end-of-line operations while improving load integrity throughout the distribution cycle, and the Little David PackPoint case packaging system–a compact solution that automates labor-intensive packaging tasks. “It is designed to consolidate five job functions–case forming, packing, sealing, printing, and labeling–into one unit,” Hantke notes.
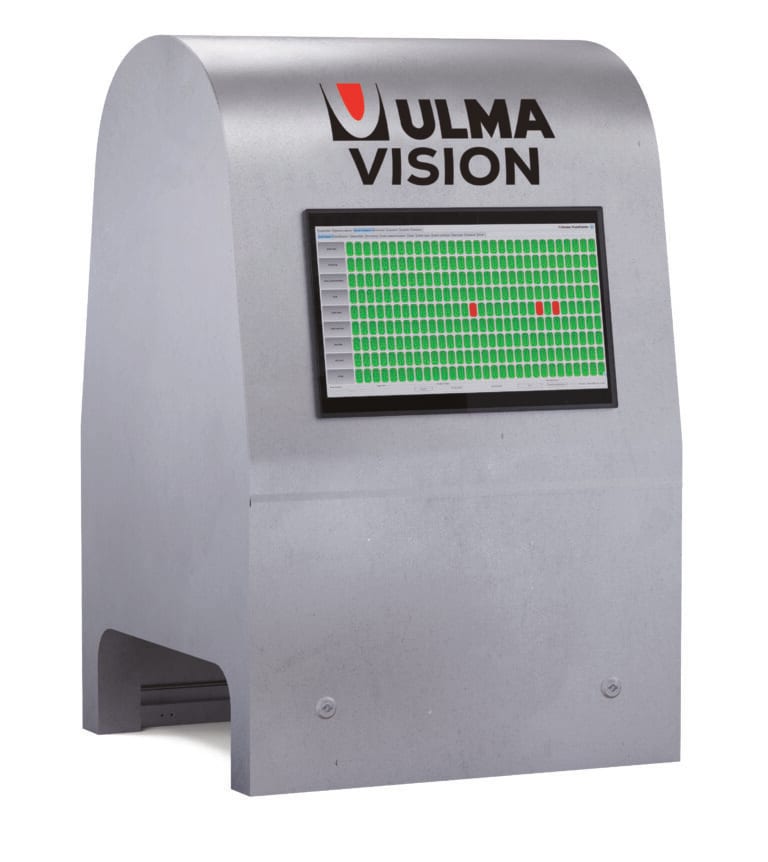
Courtesy of Harpak-ULMA Packaging
New vision systems are aimed at improving product inspection. Harpak-ULMA Packaging has introduced ULMAVision Systems, which improve quality control in bakery and snack operations for inline or standalone use, according to Josh Becker, bakery and confection segment manager. “With capabilities such as film, print, and barcode inspection powered by intuitive software, ULMA Vision ensures package quality and compliance while supporting sustainability goals.” A seal inspection feature ensures that no packages with poor seal quality are shipped.
Looking ahead
What packaging innovations do manufacturers see in the near future? Becker expects to see more improvements in vision inspection systems. “The assistance of AI has dramatically increased what is possible. Beyond evaluating product and package quality, vision inspection will improve automated packaging solutions, especially where pick-and-place robotics are involved.”
Turner sees continued advances in automation, with more sophisticated HMIs offering greater levels of guidance and control. “Enhanced safety features, such as radio frequency identification (RFID) login systems to prevent unauthorized changes, and improved cleaning mechanisms, will continue to evolve. In addition, we will see further integration of smart technologies for real-time monitoring and predictive maintenance, further boosting efficiency and reducing downtime.”
“Retailers are moving away from direct store distribution (DSD) trays and into corrugated cases due to the challenges and costs involved.”
— Dale Andersen, president/CEO, Delkor Systems
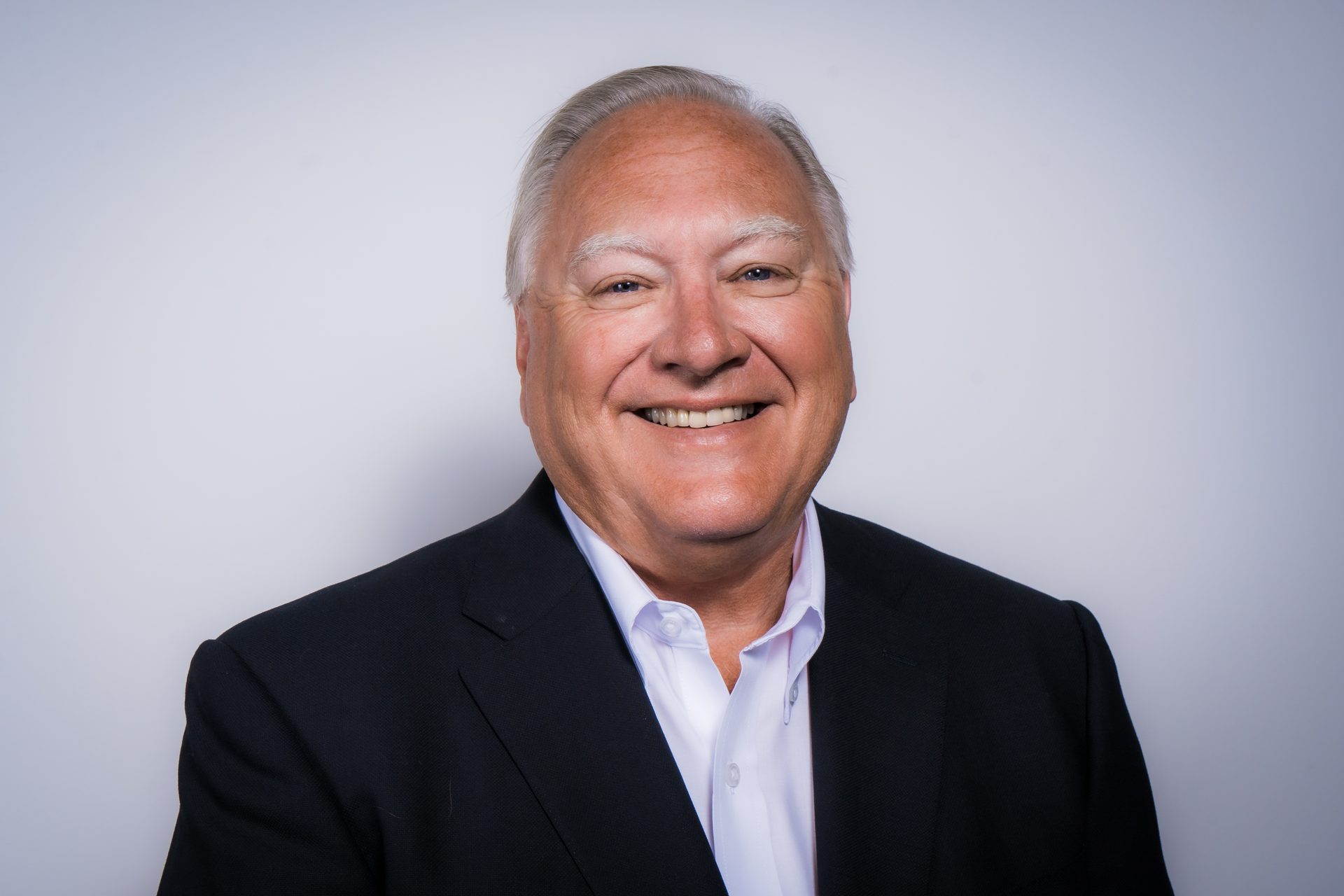